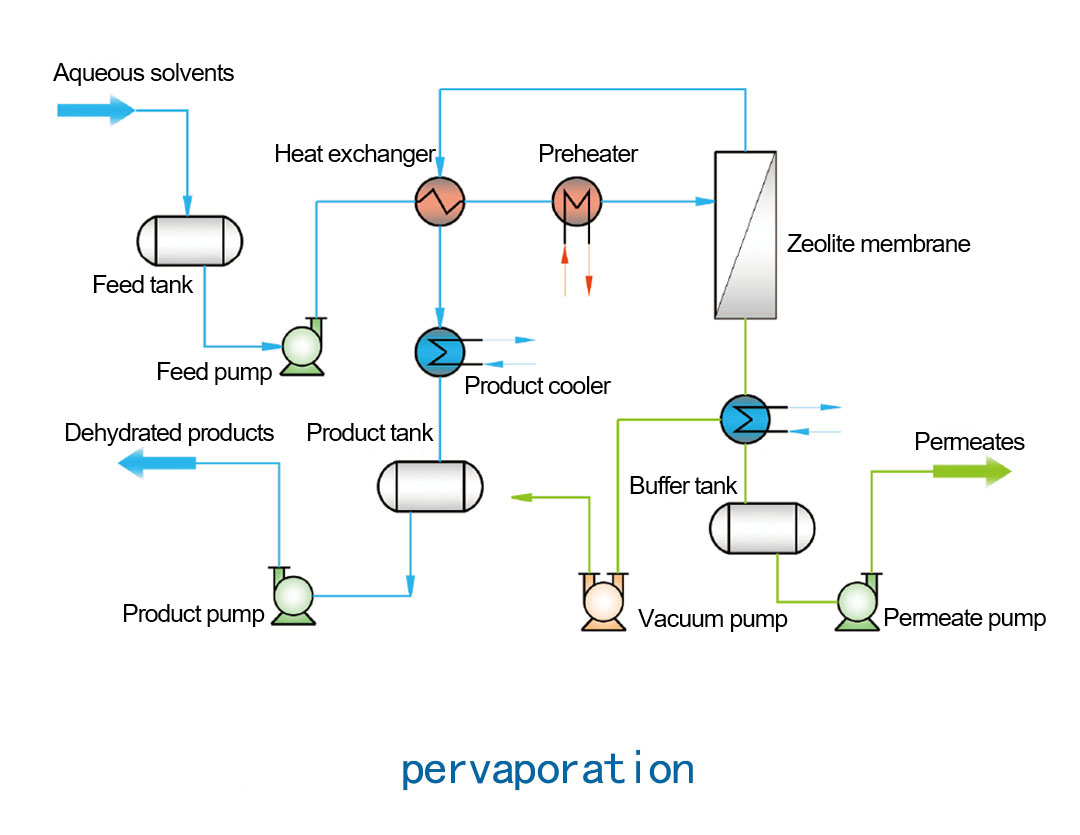

● For the mother liquor recycling in the refining process of pharmaceutical industry, our patented technology, SISIR (Solvent & Intermediate Simultaneously Recovery process), can realize the simultaneous recovery of both solvent and high value intermediates.
● Our unique process, HiPLoT-PV (High Pressure Low Temperature Pervaporation), is suitable for t high efficiency and ultra-deepdehydrationof liquefied gas.
Application fields
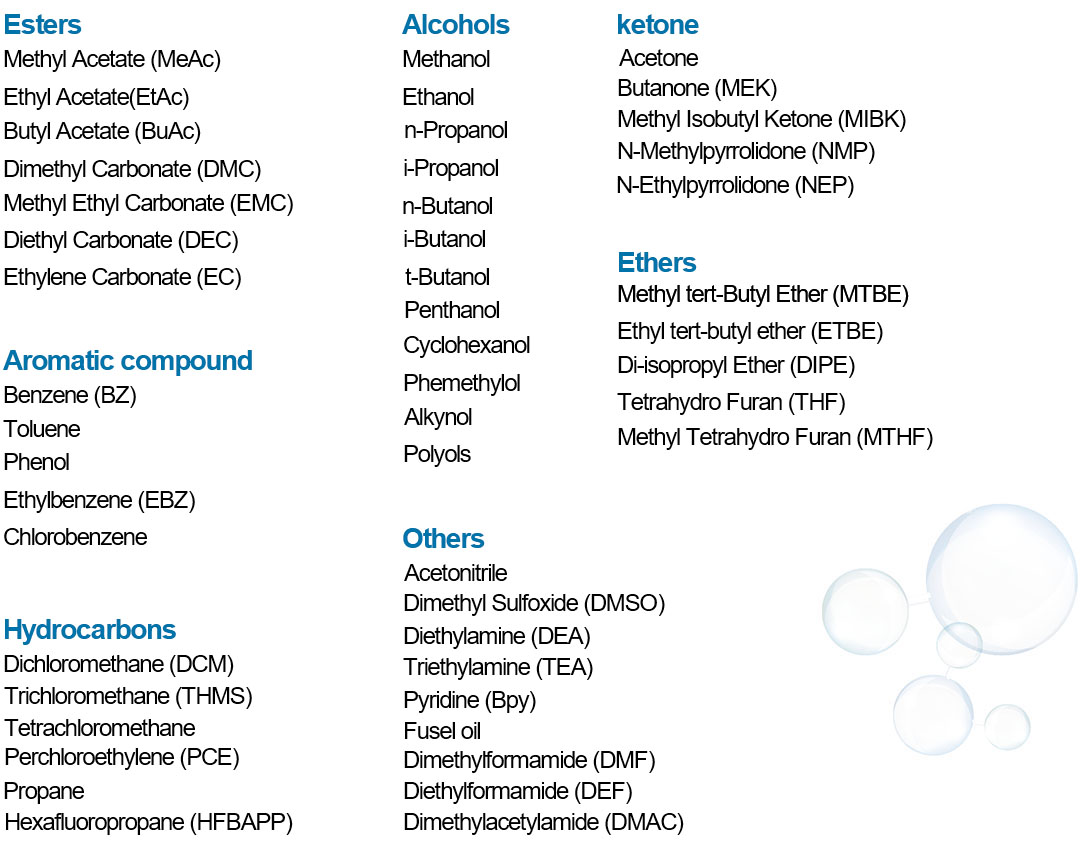
Typical alcohol-water separation performance table
Component | feed content(alcohols) | temperature(oC) | separationfactor | Throughput(kg/m2h) |
Methanol | 90.0wt.% | 60 | >10000 | 0.62 |
Methanol | 99.0wt.% | 100 | >1000 | 0.50 |
Ethanol | 90.0wt.% | 60 | >10000 | 2.37 |
Ethanol | 90.0 wt.% | 120 | >10000 | 4.62 |
Ethanol | 98.0 wt.% | 120 | >10000 | 1.85 |
n-Propanol | 90.0wt.% | 60 | >10000 | 2.69 |
i-Propanol | 90.0wt.% | 60 | >10000 | 2.55 |
n- Butanol | 90.0wt.% | 60 | >10000 | 2.80 |
t- Butanol | 90.0 wt.% | 60 | >10000 | 2.66 |
Glycol | 13wt.% | 120 | >10000 | 10.0 |
Specifications
Item | Content |
Feed conditions | Capacity | Annual output: 50 t ~ 300000 t |
Feed conditions | vaporphase / liquid phase |
Raw material composition | Water content: 100pm-50wt% |
pH | 6-8 |
conductivity | <10 us·cm-1 |
Other conditions | Free of substances that may contaminate the membrane(Hymater can provide solutions). |
Operating conditions | operating pressure | Feed side | 0.1-1.4MPa.A |
Permeate side | 100~8000Pa.A |
Product parameters | operating temperature | 0-200℃ |
operating mode | BatchBatch-wise / continuous |
Product index | Water content: could be as low as 5ppm |
Single pass recovery rate | 99.8%~100% |
Impurity introduction | No metal ions introduced. |
Typical case
i- propanol
Item | Low pressure steam / yuan | Power / yuan | Circulating cooling water/yuan | chilled water/yuan | Sum |
Distillation | 620 | 20 | 37 | --- | 677 |
Adsorption | 350 | 60 | 20 | --- | 430 |
Pervaporation | 87 | 26 | 4 | 9 | 126 |
1、Accounting example (2000 tons per year, the content of i-propanol increases from 85 % to 99.9 %)
2、The steam is RMB 200 Yuan/ t, the electricity is 0.7 Yuan/ kWh, the cooling water is 0.35Yuan/ t, and thechilled water is 1 Yuan/ t.
3、The data listed in the table are Yuan / t raw materials.
Acetonitrile
Item | Low pressure steam / yuan | Power / yuan | Circulating cooling | chilled water/yuan | Sum |
Distillation | 460 | 30 | 15 | --- | 505 |
Pervaporation | 100 | 14 | 1 | 5 | 120 |
1、Accounting example (4000 tons per year, the content of acetonitrile increases from 80% to 99.5%)
2、The steam is RMB 200 Yuan/ t, the electricity is 0.7 Yuan/ kWh, the cooling water is 0.35 Yuan/ t, and thechilled water is 1 Yuan/ t.
3、The data listed in the table are Yuan / t raw materials.
Tetrahydro Furan
Item | Low pressure steam / yuan | Power / yuan | Circulating cooling water/yuan | chilled water/yuan | Sum |
Distillation | 400 | 25 | 20 | --- | 445 |
Pervaporation | 60 | 12 | 12 | 6 | 90 |
1、Accounting example (800 tons per year, the content of Tetrahydro Furan increases from 80% to 99.5%)
2、The steam is RMB 200 Yuan/ t, the electricity is 0.7 Yuan/ kWh, the cooling water is 0.35 Yuan/ t, and thechilled water is 1 Yuan/ t.
3、The data listed in the table are Yuan / t raw materials.
10t/day Preparation of 99.5% anhydrous ethanol from 95% ethanol
Item | Azeotropic distillation technology | zeolite membranetechnology |
Annual processing capacity | t/year | 3300 |
Steam
| yuan/t product | 440 | 92 |
circulating water | yuan/t product | 19 | 18 |
electric energy | yuan/t product | 8 | 10 |
Azeotropicentrainer | yuan/t product | 50 | 0 |
Depreciation of membranes (5 years) | yuan/t product | 0 | 58.8 |
Depreciation of equipment (10 years) | yuan/t product | 40 | 31.5 |
Unit product operation cost | yuan/t product | 557 | 210.3 |
Total operating energy consumption (10,000 yuan / year) | | 183.8 | 69.4 |
Total income (10,000 yuan / year) | | 114.4 |
Price of equipment (10,000 yuan) | | 130 | 200 |
Increase in investment (10,000 yuan) | | 70 |
Payback period of investment | | 223 |